加工新型含铝复合材料的切削刀具
2017-07-12 | 编辑:中机教育网 | 来源:中国机械工业联合会机经 | 浏览量:
为了提高成品零件的性能,使其重量更轻、强度更高,并获得其他特定属性,各种新的工件材料正被不断开发。为了加工这些新材料,切削刀具必须适应其极具挑战性的加工特性。
用于加工三种含铝复合材料:铝化钛、高硅铝合金和铝—锂合金的切削刀具就集中体现了这一特点。虽然这些材料算不上是真正的“新冶材料,但为了创造对“新冶材料的市场需求,需要进行多年(有时甚至数十年)的加工应用工作。在为提高成品零部件的性能而改变工件材料的冶金特性时,通常会导致材料的可加工性下降。
铝化钛(TiAl)
铝化钛(尤其是γ-TiAl)主要用于制造喷气发动机的涡轮叶片,它可以使新一代的发动机重量更轻、燃油效率更高。TiAl材料在汽车上的应用(如制造涡轮风扇、发动机气门等)也引起人们越来越大的兴趣。一家瑞典的3D打印企业Arcam AB公司正在研究利用3D打印技术为汽车行业制造TiAl涡轮增压器。
加工TiAl材料(其钛含量和铝含量大约各为50%)的主要困难在于它既有很高的硬度,又有极好的耐磨性。此外,它对切削条件也非常敏感,其表层或次表层极易开裂。
工具制造商山高刀具公司培训和技术服务经理Don Graham指出:“加工TiAl时,通常需要采用刃口锋利的刀具,以尽量减小工件的表面破损。还有一个矛盾的问题:为了避免挤压工件表面和产生裂纹,可能需要采用较小的切深;但与此同时,为了使切屑能吸纳和带走尽可能多的切削热,用户又希望能增大切屑厚度。”
为了达到平衡,在立铣加工TiAl工件时,可采用相对较高的表面切削速度(如30m/min,但与加工钢和铸铁相比,这一速度相对较低)以及使用更锋利的切削刃。这就需要以小的切深进行切削,但又不能过小,以免切削刃温度过高。
既然加工TiAl材料成本高、难度大,为何发动机制造商仍然愿意使用它呢?Graham解释说:“首先,TiAl材料很轻;其次,它具有非常好的高温性能;第三,可以用TiAl替代Inconel合金制造工作温度极高的发动机后端,而它的重量仅为Inconel合金的一半。冶TiAl材料能耐受喷气发动机的高温烈焰,使其成为可应用于该领域的理想材料。
工具制造商山特维克可乐满公司全球工程项目办公室经理Bill Durow也认为,TiAl材料在航空航天领域的应用前景非常好。他说:“TiAl是喷气发动机内部镍基合金零部件的理想替代材料,它的密度是镍基合金的两倍,有助于提高发动机的推力重量比。目前,TiAl已用于制造喷气发动机的低压和高压叶片。”
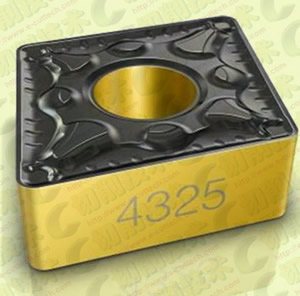
图1 TiAl车削实验所用的GC4325 CNMG刀片

图2 TiAl铣削试验所用的CoroMill300铣刀(鼠标悬浮窗口放大,单击查看放大全图)
最近,山特维克可乐满对一系列γ-TiAl锻造零件进行了切削试验。该公司的加工应用高级工程师MikeMagro说:“这种材料表面呈鳞片状,并有许多凹坑,但实际切削过程并不困难。我们用RCMT纽扣式刀片清除了表层鳞片,并用GC4325 CNMG型80度刀片进行了车削加工(见图1)。总的来说,车削试验更成功,加工出工件特征的基本形状,然后用标准的CoroCut QD刀片将其切断。我们已习惯加工航空航天业的各种难加工材料,因此切削TiAl还算不上真正的挑战。”铣削试验所用刀具为CoroMill 300铣刀(见图2)。
Magro指出,磨蚀性工件材料产生的粉尘状切屑可能会堵塞冷却液系统的过滤器。Durow说:“我们试验所用的机床配备了一个30μm的前置过滤器和一个5μm的精细过滤器,可以解决切屑堵塞问题。”他还指出,车削TiAl时,切削温度比车削镍基合金时稍高一些。车削加工TiAl的表面切削速度为40m/min,铣削加工的切削速度为33m/min,切断加工的切削速度为27m/min。
由于TiAl材料能承受高温,它在喷气发动机中的其他应用还包括一些非旋转零部件,如传统上用625 Inconel合金制造的支架。
加工诸如TiAl的一些“新”材料可能并不总需要设计新型刀具。在许多情况下,可以采用新的涂层对现有刀具进行改性。大昭和精密工具公司(BIG Kaiser Precision Tooling Inc.)Sphinx系列刀具产品经理Cory Cetkov-ic表示:“我们与刀具涂层供应商合作,确定开发新的涂层。我们把涂层供应商请到刀具库,以确定加工特定材料的最佳涂层。对于TiAl,通常采用多层涂层,例如,底层采用能提高强度的硬涂层,而顶层则采用光滑的薄涂层,以防止产生积屑瘤(BUE),并有利于排屑。”
铣削加工TiAl时,山高刀具公司推荐使用细晶粒整体硬质合金刀具(如Jabro系列立铣刀),虽然与标准立铣刀相比成本更高,但它在这种具有挑战性的加工中有更优异的性能。车削加工TiAl时,如果刀具安装可靠,工件夹持牢固,采用较大的切入角有助于减小车刀切深线处的沟槽磨损,这种磨损可能会引起刀具崩刃和加快刀具磨损进程。
Graham解释说:“如果能增大刀具的切入角度,就会有更多切削刃参与切削,并使沟槽磨损宽度分散到更多切削刃上。你可能认为,如果参与切削的切削刃增加30%,刀具寿命也将延长30%,但实际上刀具寿命可以延长四倍之多。”
由于存在刀具切深线沟槽磨损的加工挑战,许多加工车间正在试验用金刚石刀具来加工TiAl。在使用金刚石刀具时,必须降低切削刃的工作温度,以防止刀具熔解。为此,山高刀具公司建议:用热容量高的高压浇注冷却液对切削刃处进行强制冷却(如使用Jetstream Tooling冷却系统)。
航空航天供应商已对TiAl材料的加工进行了大量投资。例如,三井精机(Mitsui Seiki)已经提供了多种加工TiAl材料喷气发动机涡轮叶片的机床。目前最大的用户是日本AeroEdge公司,它使用28台专用机床来生产TiAl叶片。Mori Seiki美国公司总裁Scott Walker也认为,金刚石刀具在加工TiAl时表现优异。三井精机演示了用CVD金刚石涂层刀具加工TiAl的实例:切削速度100m/min,主轴转速3979r/min,每齿进给量0.04mm,进给率637mm/min,粗加工走刀步距0.5mm,精加工走刀步距0.4mm。每把刀具价格475美元,不过,由于金刚石刀具成本较高,三井精机的大多数用户还是选用刃口非常锋利、涂覆硬涂层的硬质合金刀具来加工TiAl材料。
肯纳金属公司产品工程高级工程师Edwin Tonne指出,γ-TiAl具有极高的加工硬化倾向,提高切削速度会显著增加其硬度。在一次切削试验中,当切削速度稍有提高时,工件的布氏硬度就马上从320增大到400。
Tonne指出:“可实现经济刀具寿命的合理切削速度大约为30-40m/min,比切削Ti6-4钛合金时大约低30%-40%。需要使用具有大前角和大后角的刀片,如果采用的每齿进给量超过0.1mm,就有可能发生崩刃,甚至损坏刀具。如果将每齿进给量保持在0.1mm以下,就能在安全的切削条件下进行加工,刀具只会出现正常的后刀面磨损。”
由于TiAl的含铝量较高,另一个问题是有些刀具涂层与铝具有化学亲和力,从而会造成一些加工问题。为此,Tonne建议采用硼化钛涂层,这种涂层可使刀具切削刃保持锋利,并且与铝没有化学亲和力。
保持较小的径向吃刀量(接触弧长)有助于改善TiAl的可加工性。Tonne说:“如果径向吃刀量保持在10%(即小的切削宽度),就可以采用更高的切削速度和进给率。冶他指出,使用肯纳公司专为加工铝合金而设计的7745 VOD-441刀片和7713 VR-701纽扣铣刀可以成功实现TiAl的面铣加工。同样,XE和XER整体硬质合金立铣刀也能有效加工TiAl。

图3 山高刀具有16个切削刃的DoubleOctomill铣刀可用于铣削高硅铝合金汽车零件(鼠标悬浮窗口放大,单击查看放大全图)
新型铝合金
新型铝基材料在其他方面的应用也在取得进展。高强度铝合金正被用于制造更多的汽车和航空零部件,汽车制造商已能对用难加工的高硅铝合金制成的发动机缸体和缸盖进行面铣、钻削和铰削加工。
纯铝重量轻、硬度低,但添加碳化硅和其他形式的硅以后,其强度、硬度、刚度和寿命都显著提高。但是,硅的加入也增大了其磨蚀性,硅的含量越高,铝合金的磨蚀性也越强。例如,Reynolds 390铝合金的碳化硅含量为17%-19%,因此具有极强的磨蚀性。
金刚石刀具或硬度极高的微晶整体硬质合金刀具是加工高硅铝合金的首选。不过,在此类材料的加工中,金刚石刀具有更明显优势。即使是硬度极高的硬质合金牌号,其刀具寿命也非常短(大约3-5min),与之相比,金刚石刀具的寿命可达1h。
这些高硅铝合金汽车零件的加工通常需要采用大直径铣刀。山高刀具公司将其有4个硬质合金切削刃的Quattromill铣刀和16个切削刃的Double Octomill铣刀应用于这种加工(见图3)。
山高刀具公司先进材料产品经理Aaron-Michael Eller指出,硅铝合金的可加工性与其含硅量成反比,硅铝合金的种类很多,含硅量通常决定了其机械加工性能。
由于铝合金硬度较低,因此很容易产生BUE(即工件材料粘附在刀具切削刃上形成积屑瘤),造成工件表面光洁度变差和刀具寿命缩短。刀具上的积屑瘤也可能沉积在工件上,当积屑瘤从切削刃上掉落时,可能会从刀具上带走一些材料颗粒,并导致刀具提前失效。
由于存在形成积屑瘤的潜在风险,山高公司建议采用刃口锋利和轻度制备的正角硬质合金刀具和光滑的高光洁涂层来加工高硅铝合金。Eller解释说:“正角刀片使我们能剪切而不是推挤(或拖曳)低硬度工件材料(使用负角刀片时有时会发生这种情况)。光滑涂层可以改善润滑性能,使切屑能从切削刃处流畅排出。对刃口的倒棱制备可以增强抗衡材料磨蚀性所需的强韧性。”
为了尽可能保持切削刃的锋利度,聚晶金刚石(PCD)刀具的刃口制备得非常锋利,并且不使用涂层。加工高硅铝合金时,采用亚微米晶粒结构的PCD牌号也可以减轻积屑瘤的影响。
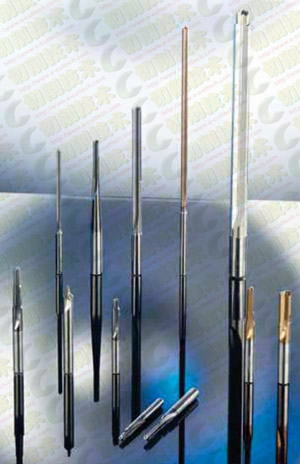
图4 采用先进涂层的专用Sphinx Quadro Plus步进式钻头可在新型铝合金的大批量加工中发挥最佳性能
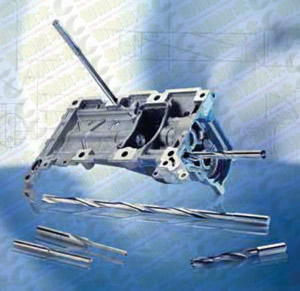
图5 使用Sphinx Quadro系列深孔钻头(产品编号52100和52150)可实现对AlSi10Mg(Cu)铸铝件的高效钻削(鼠标悬浮窗口放大,单击查看放大全图)
BIG Kaiser公司的Cetkovic指出,与加工TiAl一样,采用新型刀具涂层也可以改善高硅铝合金的切削性能。“我们用Sphinx标准刀具加工硅铝合金,并利用新开发的创新涂层来提高切削性能和刀具寿命。冶与每把未涂层刀具只能加工5个零件相比,每把涂覆了新型涂层的刀具可加工250个零件。同样,这种多层涂层的底层为高强度硬涂层,外层则为能改善排屑性能并有助于防止积屑瘤的光滑涂层。
Cetkovic说:“对于铝合金加工,我们有材质为微晶硬质合金的系列直槽钻头,这些钻头能以极高的切削速度和进给率进行钻削,而其直槽设计缩短了切屑从刀具排出必经路径的长度,从而优化了排屑性能。每把刀具通常可以加工几万个工件。冶例如,一支长径比为40/1的钻头可加工高达72,000个高硅铝合金汽车零件。
Cetkovic指出:“虽然此类刀具价格不菲,但使用它们的加工车间很清楚,自己花钱购买的并不只是钻头,而是加工出的孔。一把刀具400美元看似昂贵,但如果它能加工出72,000个孔,实际上性价比相当高。
冶铝—锂合金
在全球航空航天行业,新型铝—锂合金材料的应用正方兴未艾。这种低密度合金集重量轻、装配和维护成本低、可采用先进焊接技术(如摩擦焊)等优势于一身。较低的合金密度和优良的材料特性使航空制造业可以优化飞机的结构设计,用它设计的航空结构件可以减重25%,而飞机重量的减轻可以降低油耗和减少CO2排放。
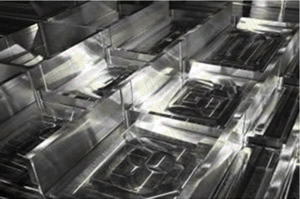
图6 用Constellium公司生产的Airware合金制造的喷气机翼肋板(鼠标悬浮窗口放大,单击查看放大全图)
全球主要的铝—锂合金材料供应商之一是总部位于巴黎的Constellium公司,为了支持航空项目的技术创新,该公司经过几十年的持续研发,成功生产出了Airware高性能铝—锂合金。2010年开始全面供货的Airware合金非常适合用于制造各种主要的航空结构件(见图6)。除了铝和锂以外,Airware合金中还包含作为主要添加元素的铜和银。
Constellium公司客户应用工程总监Sylvain Henry介绍说:“由于Airware合金具有更好的抗疲劳和抗腐蚀能力,可以提高飞机构件的耐用性,从而使航空公司能够延长其维修间隔时间。Airware合金能无限次回收利用,其材料性能不会有任何损失,有利于航空航天工业的可持续发展。冶他指出,Airware合金已在一些重要的航空项目(如空客A350 XWB和庞巴迪C系列)中得到应用,并已获选用于一些航天项目(包括Space X公司的猎鹰9号火箭和洛克希德·马丁公司的猎户座航天器)。
Constellium公司在法国Is-soire兴建了Airware合金铸造厂,目前该厂已通过了Constelli-um公司主要客户的资质认证。
与其他铝合金一样,Airware合金也需要进行一些标准的机加工,如轮廓加工、表面加工、凹腔加工和零件精加工。这些加工通常在标准机床(如高速和标准速度的立式、卧式加工中心)上进行。
Henry说:“Airware材料包含一系列硬度较高的合金,因此其加工可能与其他硬铝合金略有不同,但差异并不是很大。我们的一些加工合作伙伴开发了专用刀具,以确保获得与加工其他硬铝类似的生产率水平。加工Air鄄ware时会产生大量切屑和废料,如果将这些材料有效地分离回收,则可将其重新应用到制造过程之中。”
上一篇 上一篇:无人驾驶汽车应走得更“稳”一些
下一篇 下一篇:华润曹妃甸百万火电3号机组发电机定子顺利就位