如此之轻——3D打印应用于液压动力单元
2018-09-18 | 编辑:中机教育网 | 来源:中国机械工业联合会机经 | 浏览量:
3D打印液压元件,液压阀块已经在走进我们的生活,而制造商们也正琢磨着3D打印会否给液压动力单元带来些好处,并逐渐引起了他们的兴趣。
液压动力单元其中一个很重要的优势就是具有极高的功率重量比-极小规格尺寸的单元可以传递很高的功率。这也就是液压动力单元在一些移动工具依然如此广受重视的原因,比如在救援设备等,其便于携带,提供的压力高,便于剪切或扩张操作等。
高压液压动力单元,特别是移动液压工具制造商正在追寻的就是:动力单元尽可能的轻。设计师们似乎想尽了一切办法-集成动力单元采用插装阀而不是管式阀,尽可能减少元件数量,管路尽可能的短……。然而他们发现,也许只有3D打印,才是他们想要的!
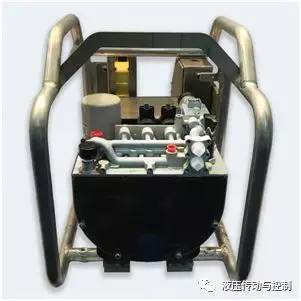
图示动力单元可提供较高功率的动力。由于其需要携带至现场,设计师希望其足够轻。几番传统设计方案更改后,他们决定采用3D打印技术,其阀块重量大约只是原来的1/4。(Aidro hydraulic提供图片)
3D打印元件的优势
金属3D打印并不是一门新科技,但是直到现在,随着材料强度的增加,使其能够承受高压力的需求,才使得液压领域逐渐引入这门技术。金属3D打印经常与增材制造相关。增材制造起始于一无所有,然后通过逐渐增加适量材料,使得元件满足外观,尺寸以及机械性能等方面的要求。
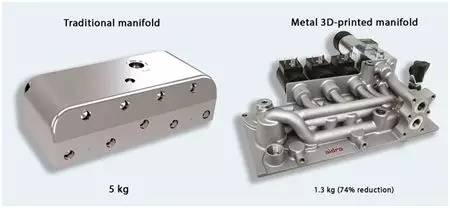
3D打印阀块更小,更轻!
左图为传统方法设计和制造的阀块,右图为3D打印设计和制造的阀块,其减重达25%。(Aidro hydraulic提供图片)
这可以从加工制造方法上进行比较。传统的阀块加工均起始于金属块,然后通过去除材料满足应用需求。这种技术的缺点就是,为了减少加工成本,阀体通常会留有更多材料,导致阀块比实际需要的重。虽然多余的材料可以通过加工方式去除,但是如果去除多余的材料,也会增加后续的制造成本。这种重量的减少与成本的增加相比,显得就没有那么重要了。
而且,传统加工制造还局限于不能制造期望的几何构造,诸如椭圆形或者方形的流道,其与圆形流道相比,在通流量一样的情况下,更节省空间。传统方法的加工必须保证孔道的定位互相不干涉或者穿孔,因此孔道之间会留有足够的壁厚,从而保证强度。为了使内部孔道保证必要的互联,需要设计、加工很多辅助孔,最后必须采用工艺堵堵上。
金属3D打印逐层建立所需要的元件。通过计算机控制激光,熔融各层金属,构造所需几何形状。液压3D打印经常采用的技术包括粉体熔化成型技术(Powder Bed Fusion) ,或者直接金属激光烧结(Direct Metal Laser-Sintering,DMLS),或者选择性激光熔融(Selective Laser Melting,SLM)。
DMLS是通过使用高能量的激光束再由3D模型数据控制来局部熔化金属基体,同时烧结固化粉末金属材料并自动地层层堆叠,以生成致密的几何形状的实体零件。DMLS适用于多种合金,允许功能样品与批量成品采用同一种材料。
SLM技术是利用金属粉末在激光束的热作用下完全熔化、经冷却凝固而成型的一种技术,用它能直接成型出接近完全致密度的金属零件。SLM完成的元件因为通过控制金属成品的晶体结构而具有更高的强度。
此外,3打印可利用更小的空间,流道的设计可以获得更大的流量。内部孔道的互联不必要从外部加工,消除了使用工艺孔堵的可能。
金属3D打印阀块用于动力单元
Aidro hydraulic利用该技术在移动动力单元中制造了紧凑、轻量型阀块。结果就是阀块只是传统工艺制造阀块重量的1/4。3D打印阀块既可以适应之前阀块的安装尺寸,达到减重的目的,如果新项目的需求,无论尺寸和重量,3D打印阀块都具有极大的优势。
上一篇 上一篇:中国科学家成功研制新型“可呼吸”钠-二氧化碳电池
下一篇 下一篇:京东物流大力引入机器人技术,论第一家物流企业的技术修养