体:大 中 小 探秘宝沃智能工厂 揭开智能制造的神秘面纱
2017-09-08 | 编辑:中机教育网 | 来源:中国汽车报 | 浏览量:
日前,工信部公布了2017年中德智能制造合作试点示范项目名单。德国工业4.0和中国制造2025结合的智能制造到底什么样?9月6日,带着这样的疑问,记者来到宝沃汽车位于北京的智能工厂,揭开智能制造的神秘面纱。
八车型共线是怎样实现的?
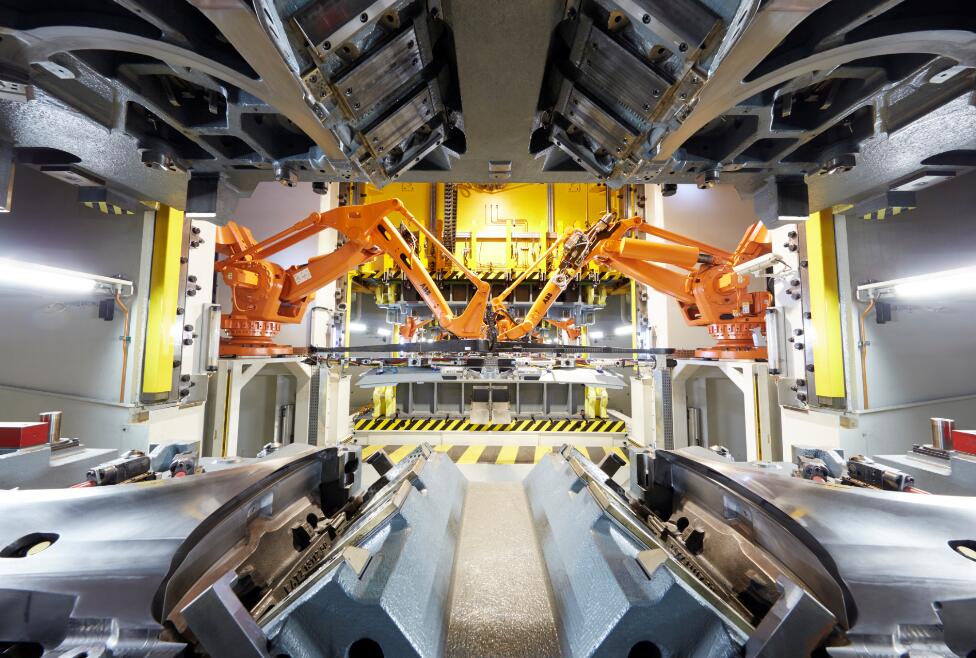
据闻,宝沃的北京工厂引入了全球首条八车型智能制造系统,具备强大的灵活性和应变能力,能在缩短产品生产周期的同时提升产品质量,最大程度实现工业4.0模式下的生产。八车型怎么在一条生产线上实现?柔性化生产线告诉你答案。
在车间,记者看到宝沃智能工厂的柔性化生产线上柔性NC系统,可根据不同车型零件精确定位,灵活打造特定工件,满足个性化车型的生产。为保证产品生产的牢固与稳定,在焊接中,宝沃采用中频一体化自动焊接技术,可实现焊接自动化率100%,在确保焊接质量的同时,也更有效地降低40%能耗。正是柔性化生产的这些特性,让宝沃的这条生产线可最高达到八车型共线上产,而且还可以根据用户需求,进行定制化车型生产及开发,满足更多的个性化需 求。
作为柔性化生产线的好搭档,数字化工厂系统为宝沃工厂的智能制造提供了大数据支撑。构建数字化系统,虚拟环境下模拟工厂生产运营,降低宝沃汽车从设计到生产制造之间的不确定性,从而缩短产品设计到生产的转化时间,提高产品的可靠性。大数据贯穿“前期研究——概念开发——设计工程——工程开发与产品验证——生产准备——试销+批产”每一个环节,让智能制造更“靠谱”。
举个例子,在前期研究中,针对客户“个性化点单”,数字化工厂可定义整车“颜色管理方案”等支持未来个性化销售要求,而在工程开发与产品验证阶段,CAE 仿真管理平台,可集成行业分析软件(如:Autoform、Ls-dyna、Altair HyperWorks等)开展虚拟验证,有效降低实车验证成本,形成宝沃“虚拟+实车”双重验证体系;在生产准备中,则以产品数据、工艺数据和设备数据为基础进行工艺规划,基于三维虚拟环境对整车生产过程进行仿真、评估可行性和优化制造过程,降低制造成本,提升宝沃数字化工艺水平。
智能工厂不仅在柔性化和数字化方便彻底颠覆传统的生产制造,在冲压、车身、总装等固有制造工艺上也有不同程度的智能性提升。宝沃智能化工厂的冲压车间,采用全球一流的整线高速伺服自动化生产线,自动化程度100%,宽工艺范围+高精度, 整线节拍达到15SPM(冲次/分钟)。冲压车间主线采用全自动高精度焊接生产工艺,运用双总拼及顶盖激光钎焊等高精技术,标准化工艺流程可实现同一车型在不同工厂快速导入。总装车间采用国际先进网络化扭矩实时控制系统及网络化电检系统,全面提升整车质量,这正是“h”型柔性生产线的魅力。
智能工厂更绿色
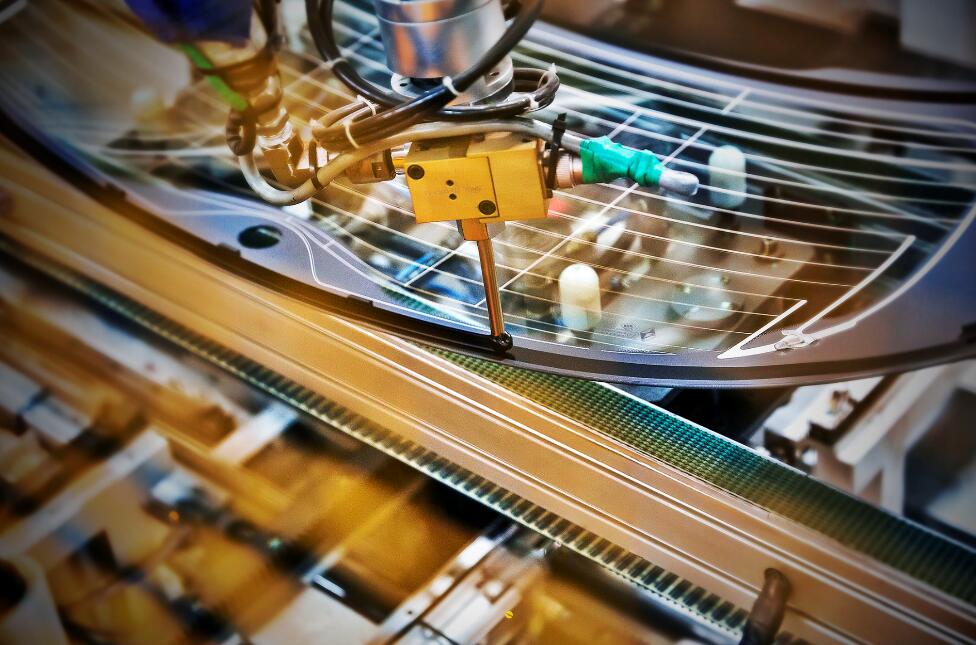
智能化工厂在提升生产品质和效率的同时,更增添了很多亮色。其中,油漆车间环境友好型水性漆+免中涂工艺体系,与豪华轿车相同的油漆材料,漆膜质量安全可靠;沸石转轮+RTO废气处理方式,VOC去除率≥98%,高效节能环保。不仅达到了北京堪称全国最严的环保要求,也为工厂节省了环保成本。
在生产线上追求绿色的同时,宝沃的智能工厂还在寻求更多的节能环保。据了解,宝沃智能工厂还规划了太阳能系统,系统建厂后,满荷运转可为工厂提供20%的用电量。
九屏一云打造智能用车生态服务
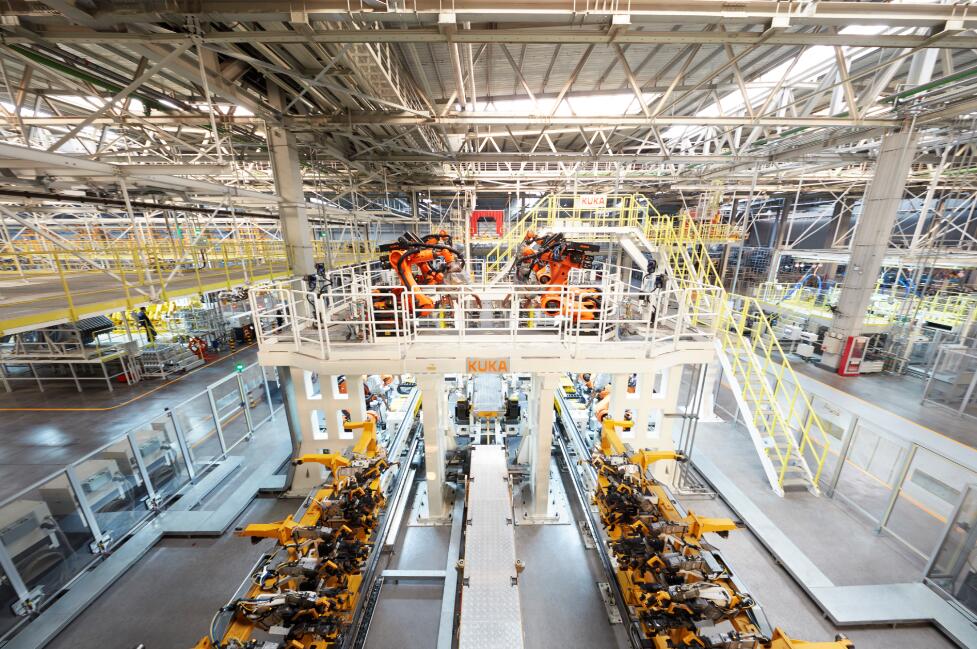
宝沃“九屏一云”服务平台(Screen9 Service Platform)是宝沃汽车“资源链合,互联共享”商业模式的又一实践。宝沃通过B-Cloud宝沃云,以大数据为基础,同时转动“消费链+”和“产业链+”,最终实现从传统B2B2C到以用户为中心的B2C2B智能用车生态服务。九屏,即TV终端、PC终端、手机终端、车机终端、销售终端、售后服务、生产终端、呼叫终端、总监控终端,这些“屏幕”连接到宝沃云上,实现智能联动,进行广泛的数据抓取及分析,并定向追踪目标用户,实时掌控其驾驶需求,并为用户提供整车“全生涯周期”管理及客户“全生涯周期”服务,努力为用户提供更加契合需求的出行解决方案。
上一篇 上一篇:中国车企加紧布局东盟市场
下一篇 下一篇:福田汽车8月销售新能源汽车1343辆 同比增长88.58%